- Die Prozessschritte beim Härten und Vergüten
- Einsatzhärten
- Carbonitrieren
- Schwarzoxidieren
- Vakuumhärten (Niederdruckaufkohlen)
- Randoxidationsarmes Härten und Vergüten
- Restaustenitumwandlung mit flüssigem Stickstoff (Tiefkühlen – Kryogene Behandlung)
- Allgemeine und häufig gestellte Fragen zum Härten und Vergüten
Die Prozessschritte beim Härten und Vergüten
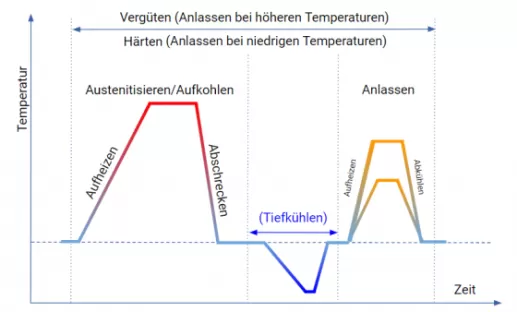
Alle Prozessvarianten weisen die folgenden Prozessschritte auf:
Austenitisierung
Erwärmung auf eine werkstoffspezifische Temperatur zur vollständigen Austenitbildung. Der zum Härten erforderliche Kohlenstoff ist vor dem Härten in Karbiden gebunden. Diese zerfallen während des Austenitisierens und der freiwerdende Kohlenstoff wird im Austenitgitter gelöst. Um den Zerfall auch im Inneren des Bauteils sicherzustellen, muss das Werkstück eine Zeit lang auf Temperatur gehalten werden. Beim Einsatzhärten wird in diesem Schritt der Kohlenstoffgehalt in der Randschicht erhöht. Die Austenitisierungstemperatur muss mindestens 30°C über dem Umwandlungspunkt liegen.
Abschrecken
Das Abkühlen von der Austenitisierungstemperatur muss mit einer werkstoffspezifischen Mindestgeschwindigkeit stattfinden, um die diffusionsgesteuerte Ausbildung von Gleichgewichtsphasen zu verhindern. Durch das Abschrecken bleibt der im Austenit gelöste Kohlenstoff bei der Umwandlung in die kubisch-raumzentrierte Gittermodifikation (Ferrit) zwangsgelöst und weitet dieses Gitter tetragonal auf (Martensit). Martensit ist sehr hart und spröde.
Zum Erreichen der angestrebten Abschreckgeschwindigkeit spielt das Abkühlmedium eine entscheidende Rolle. Die Auswahl richtet sich unter anderem nach Werkstoff, Geometrie, Querschnitt und der gewünschten Härte.
Die wichtigsten Abschreckmedien sind
Luft (Gase) → Polymere → Öl → Salz →Wasser
------------------------------------------------------->
Abschreckintensität
Anlassen
Anlassen ist eine dem Härteprozess nachgeschaltete thermische Behandlung, um die Zähigkeit und die Härte auf die gewünschten Werte einzustellen. Nach dem Härten wird der Stahl bei relativ niedrigen Temperaturen im Bereich zwischen 200 und 400 °C angelassen. Beim Vergüten liegen die Anlasstemperaturen im Bereich zwischen 550 und 700 °C. Anlassfarben entstehen, wenn das Anlassen unter Sauerstoffeinfluss durchgeführt wird. Es erfolgt eine Oxidschichtbildung, deren Dicke und Farbe durch die Temperatur bestimmt wird.
Eingesetzte Schutzgase, insbesondere bei hohen Anlasstemperaturen:
- Stickstoff
- Wasserstoff
Restaustenitumwandlung
Restaustenitumwandlung ist die nachträgliche Umwandlung von im Werkstück verbliebenem Restaustenit nach dem Härten in Martensit. mehr
Einsatzhärten
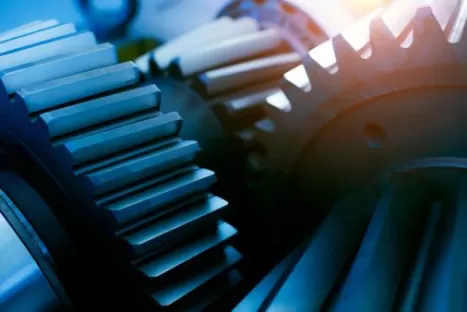
Beim Einsatzhärten von Stahl wird der Randbereich während der Austenitisierung mit Kohlenstoff angereichert. Beim Abschrecken erfolgt in der Randschicht die Martensitbildung, während der Kern seine Duktilität behält.
Hier werden Schutzgase eingesetzt, die in der Lage sind, Kohlenstoff an die Werkstücke abzugeben und damit den Kohlenstoffgehalt im Randbereich zu erhöhen. Klassische Schutzgase bestehen aus Stickstoff, Wasserstoff und Kohlenmonoxid (Endogas, Stickstoff-Methanol). Daneben können auch Mischungen aus technischen Gasen verwendet werden, die in ihrer Zusammensetzung an die Materialien und Ofenanlagen angepasst sind.
- Stickstoff-Methanol-Verfahren
- Endogas
- Stickstoff – Wasserstoff – Propan/Methan
Carbonitrieren
Das Carbonitrieren ist eine besondere Art des Einsatzhärtens. Neben Kohlenstoff wird gleichzeitig Stickstoff in die Randschicht eingebracht.
Das Carbonitrieren findet bei Temperaturen zwischen 750 und 930 °C statt. Die erreichbaren Tiefen hängen von der gewählten Temperatur ab.
Carbonitrieren erzielt im Vergleich zum Einsatzhärten Randschichten mit
- höherem Reibverschleiß-Widerstand
- verbesserter Anlassbeständigkeit
- und besseren Notlaufeigenschaften
Eingesetzte Schutzgase:
- Stickstoff
- Wasserstoff
- Ammoniak
- Kohlenwasserstoffe
- Endogas
Gasversorgungen:
Schwarzoxidieren
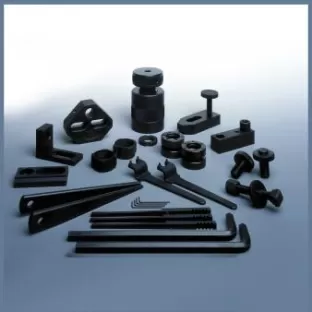
Das von Air Liquide patentierte Verfahren zum Schwarzoxidieren stellt in bestimmten Fällen durch den Verzicht auf chemische Stoffe eine kostengünstige und umweltschonende Alternative zu konventionellen Verfahren dar.
Die Einbindung in den Härteprozess ergibt durch den Wegfall von Nachbehandlungen in der Summe eine Zeitersparnis, da der Prozess mit geringem Investitionsbedarf in bestehende Ofenanlagen integriert werden kann.
Während der Wärmebehandlung wird am Ende der Austenitisierungsphase ein Atmosphärenwechsel vollzogen, der in einer definierten Kurzzeitoxidation zur Ausbildung einer geschlossenen Fe3O4-Schicht führt. Die Poren der Oxidschicht werden im Ölbad getränkt. Dadurch weisen die Schichten einen temporären Korrosionsschutz auf.
Mit der Nutzung vorhandener Mess- und Regeleinrichtungen ist die Einbindung und Reproduzierbarkeit des Prozesses sichergestellt.
Eingesetzte Schutzgase:
- Stickstoff
- Wasserstoff
Gasversorgungen:
- Stickstoff-Versorgung
- Wasserstoff-Versorgung
Vakuumhärten (Niederdruckaufkohlen)
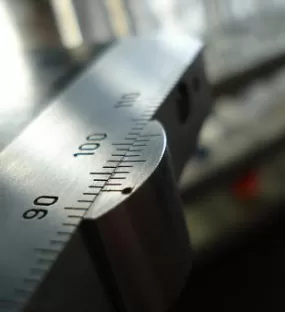
Das Niederdruckaufkohlen (Vakuumhärten) ist ein Vakuumwärmebehandlungsverfahren, das die Härte im Randbereich der Werkstücke durch das Einbringen von Kohlenstoff erhöht. In den meisten Fällen kommt als Aufkohlungsmittel Acetylen zum Einsatz.
Die Niederdruckaufkohlung ist mit einer Hochdruckgasabschreckung gekoppelt, die – abhängig von den Gasversorgungsbedingungen – hohe Kühlraten sicherstellt.
Als Abschreckgase werden meist Stickstoff oder Helium
eingesetzt.
Eingesetzte Gase beim Niederdruckaufkohlen (Vakuumhärten):
- Acetylen
Eingesetzte Gase zum Hochdruckabschrecken:
- Stickstoff
- Helium
- Argon
Gasversorgungen:
Randoxidationsarmes Härten und Vergüten
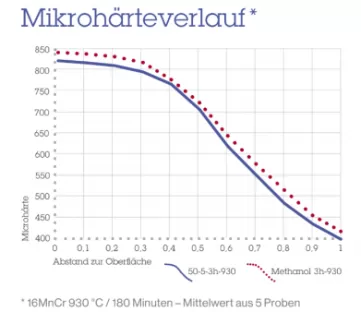
Klassische Atmosphären zum Härten und Vergüten weisen mehr oder weniger hohe Gehalte an beispielsweise Kohlenmonoxid auf. Das damit eingebrachte Sauerstoffpotenzial kann zu einer selektiven Oxidation sauerstoff-affiner Legierungselemente führen. Durch die Oxidation der Legierungselemente während der Wärmebehandlung stehen diese beim Abschreckvorgang nicht mehr für die Gefügeausbildung zur Verfügung.
Die Begasung mit auf Werkstoff und Ofenanlage zugeschnittenen sauerstoff-freien Gasmischungen ermöglicht die Verwendung bestehender Härte- oder Vergüteanlagen, mit einem überschaubaren Versuchsaufwand.
Unter Einhaltung der Formierzeiten der Ofenanlage können die Werte für die Randoxidation auf < 5 μm reduziert werden.
Eingesetzte Schutzgase:
- Stickstoff
- Wasserstoff
- Kohlenwasserstoffe
Restaustenitumwandlung mit flüssigem Stickstoff (Tiefkühlen – Kryogene Behandlung)
Bei bestimmten Werkstoffen wird beim Härten nicht der gesamte Austenit in Martensit umgewandelt. Restaustenit im Werkstück ist weich und instabil, mit der Tendenz sich später in Martensit umzuwandeln.
Die Maßhaltigkeit eines Werkstückes ist dadurch in Frage gestellt, da Martensit ein bis zu 1% größeres Volumen hat als Austenit. Daher ist für viele Anwendungen die vollständige Restaustenitumwandlung nach dem Härten zwingend notwendig.
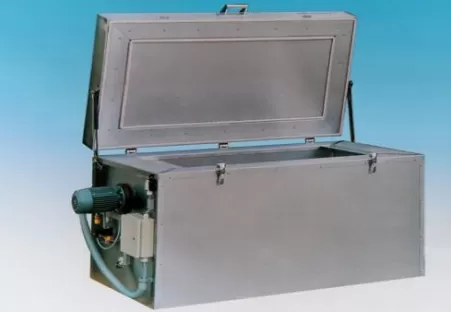
Der Anteil an Restaustenit kann zum einen durch mehrmaliges Anlassen gesenkt werden, zum anderen kann eine Tieftemperaturbehandlung durchgeführt werden. Diese wird in geeigneten Anlagen unter der Anwendung von flüssigem Stickstoff durchgeführt.
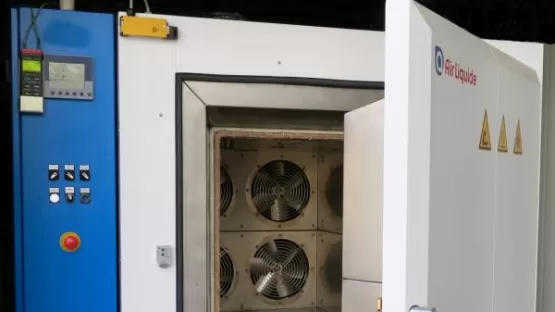
Mit Kälte-Wärme-Kammern können, durch die eingebaute Heizung, das Tiefkühlen und Anlassen ohne Umchargieren in einer Anlage durchgeführt werden.
Die Kammern können in ihren Abmessungen an Chargiergestelle und Ofenlinie angepasst werden.
Der Einsatz technischer Gase ist für die meisten Wärmebehandlungen unerlässlich. Die Wahl der Gaskomponenten in Art und Menge wird von vielen Faktoren beeinflusst.
Um für die jeweilige Aufgabenstellung das technologisch und wirtschaftlich beste Gasgemisch zu finden, betrachten die Wärmebehandlungs-Experten von Air Liquide im Rahmen eines Ofen-Audits alle Parameter und implementieren gemeinsam mit Ihnen die beste Lösung.
Allgemeine und häufig gestellte Fragen zum Härten und Vergüten
Was sind die grundlegenden Prozessschritte beim Härten und Vergüten?
- Austenitisierung: Erwärmen des Werkstücks, um den Kohlenstoff im Austenitgitter zu lösen. Beim Einsatzhärten wird in diesem Schritt der Kohlenstoffgehalt in der Randschicht erhöht.
- Abschrecken: Schnelles Abkühlen, um die diffusionsgesteuerte Ausbildung von Gleichgewichtsphasen zu verhindern und Martensit zu bilden.
- Anlassen: Thermische Behandlung nach dem Härten, um die Zähigkeit und Härte auf die gewünschten Werte einzustellen.
Was ist Austenitisierung und warum ist sie wichtig?
Die Austenitisierung ist das Erwärmen und Halten des Werkstücks auf eine werkstoffspezifische Temperatur, um eine vollständige Austenitbildung zu erreichen. Dadurch wird der für die Härtung erforderliche Kohlenstoff gleichmäßig im Austenitgitter gelöst. Dies ist wichtig, da der zum Härten erforderliche Kohlenstoff in Karbiden gebunden ist, die während der Austenitisierung zerfallen und den Kohlenstoff freisetzen, der sich im Austenitgitter löst.
Was bedeutet Abschrecken und welche Abschreckmedien gibt es?
Das Abschrecken ist das schnelle Abkühlen von der Austenitisierungstemperatur, um die Bildung von Martensit zu erreichen. Häufig verwendete Abschreckmedien sind Luft (Gase), Polymere, Öl, Salz und Wasser, wobei die Abschreckintensität in dieser Reihenfolge zunimmt.
Was ist Anlassen und welche Schutzgase werden dabei eingesetzt?
Das Anlassen ist eine Wärmebehandlung nach dem Härten, um die Zähigkeit und Härte des Materials einzustellen. Schutzgase wie Stickstoff und Wasserstoff werden insbesondere bei hohen Anlasstemperaturen eingesetzt, um Oxidation zu verhindern.
Was ist Einsatzhärten und welche Schutzgase werden dabei verwendet?
Beim Einsatzhärten wird der Randbereich des Werkstücks während der Austenitisierung mit Kohlenstoff angereichert. Schutzgaskomponenten wie Kohlenmonoxid und/oder Kohlenwasserstoffe werden eingesetzt, um den Kohlenstoffgehalt in der Randschicht zu erhöhen.
Was ist Carbonitrieren und welche Vorteile bietet es gegenüber dem Einsatzhärten?
Carbonitrieren ist eine spezielle Art des Einsatzhärtens, bei der gleichzeitig Kohlenstoff und Stickstoff in die Randschicht eingebracht werden. Im Vergleich zum Einsatzhärten erzielt Carbonitrieren Randschichten mit höherem Reibverschleiß-Widerstand, verbesserter Anlassbeständigkeit und besseren Notlaufeigenschaften.
Welche Schutzgase werden beim Carbonitrieren verwendet?
Schutzgase, die beim Carbonitrieren eingesetzt werden, sind:
- Stickstoff
- Wasserstoff
- Ammoniak
- Kohlenwasserstoffe
- Endogas.
Was ist Schwarzoxidieren und welche Vorteile bietet das von Air Liquide patentierte Verfahren?
Schwarzoxidieren ist ein Verfahren, das in bestimmten Fällen eine kostengünstige und umweltschonende Alternative zu konventionellen Verfahren darstellt, da es auf chemische Stoffe verzichtet. Durch die Integration in den Härteprozess wird Zeit gespart, da Nachbehandlungen entfallen.
Welche Schutzgase werden beim Schwarzoxidieren verwendet?
Was ist Vakuumhärten (Niederdruckaufkohlen) und welche Gase werden dabei eingesetzt?
Vakuumhärten ist ein Vakuumwärmebehandlungsverfahren, das die Härte im Randbereich der Werkstücke durch das Einbringen von Kohlenstoff erhöht. Acetylen wird als Aufkohlungsmittel verwendet, und Stickstoff, Helium oder Argon werden zum Hochdruckabschrecken eingesetzt.
Was bedeutet Randoxidationsarmes Härten und Vergüten und welche Vorteile bietet es?
Das Härten und Vergüten mit sauerstofffreien Gasmischungen reduziert die Oxidation sauerstoffaffiner Legierungselemente während der Wärmebehandlung. Dies ermöglicht die Verwendung bestehender Anlagen und reduziert die Randoxidation.
Was ist Restaustenitumwandlung und warum ist sie wichtig?
Restaustenit ist Austenit, der nach dem Härten im Werkstück verblieben ist und sich später in Martensit umwandeln kann, was zu Maßänderungen führen kann. Die vollständige Restaustenitumwandlung ist daher für viele Anwendungen zwingend notwendig.
Wie kann die Restaustenitumwandlung erreicht werden?
Der Anteil an Restaustenit kann durch mehrmaliges Anlassen oder durch eine Tieftemperaturbehandlung mit flüssigem Stickstoff gesenkt werden.
Wie unterstützt Air Liquide bei der Auswahl des richtigen Gasgemisches für die Wärmebehandlung?
Die Wärmebehandlungs-Experten von Air Liquide führen ein Ofen-Audit durch, um alle Parameter zu berücksichtigen und gemeinsam mit dem Kunden die technologisch und wirtschaftlich beste Gaslösung zu implementieren.