Unter Oxy-Fuel Verbrennung (Oxy für Oxygen = Sauerstoff und fuel = Brennstoff) wird der Einsatz von reinem Sauerstoff anstelle von Luft in einem Verbrennungsprozess verstanden. Dieses Verfahren wird heute in fast allen Metallbranchen eingesetzt, aber auch Unternehmen aus der Glas-, Keramik- und Chemieindustrie nutzen die Vorteile der Energieersparnis und der Emissionsminderung, die sich aus dem Einsatz von Sauerstoff in Verbrennungsprozessen im Vergleich zu Luft ergeben.
Oxy-Fuel Feuerungssysteme bestehen im Wesentlichen aus dem Brenner, der Mess- und Regeltechnik für die erforderlichen Medien sowie eventuell den notwendigen mechanischen Hilfseinrichtungen.
Grundlagen der Oxy-Fuel Verbrennung
Konventionell werden Brennstoffe wie beispielsweise Erdgas oder Öl mit Luft als Oxidationsmittel verbrannt. Für die Verbrennung von 1 m³ Methan werden 2 m³ Sauerstoff benötigt. Im Falle der Verbrennung mit Luft müssen dafür 10 m³ Luft eingesetzt werden und es entstehen 11 m³ Abgas. Bei der Oxy-Fuel Verbrennung dienen 2 m³ technischer Sauerstoff als Oxidationsmedium und es entstehen lediglich 3 m³ Abgas infolge des vermiedenen Stickstoff-Ballasts.
Damit steigen
- der feuerungstechnische Wirkungsgrad
- die maximal erreichbare Flammentemperatur
- die Verweilzeit der Verbrennungsgase im Feuerraum
- die durch Strahlung erzeugte Wärmeübertragung
- die Leistung des Prozesses
Gleichzeitig lassen sich mit der Oxy-Fuel Verbrennung der Brennstoffverbrauch und die Schadgasemissionen (CO₂, CO, NOx, SOx) wirkungsvoll senken.
Das Abgas verlässt den Feuerraum mit einer Temperatur oberhalb der Prozesstemperatur. Diese Wärme geht dem Prozess verloren, wenn keine Wärmerückgewinnung erfolgt. Die über das Abgas verlorene Wärmeenergie ist umso größer, je höher die Prozesstemperatur und je größer die Abgasmenge sind.
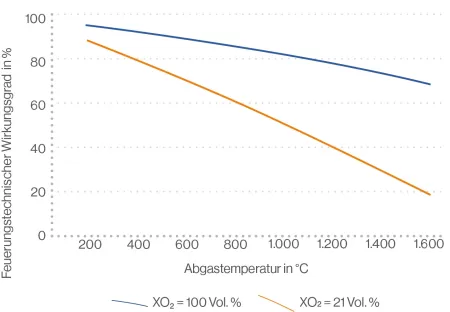
Bild 2 zeigt den Vergleich der auf die Abgastemperatur bezogenen feuerungstechnischen Wirkungsgrade für eine Erdgas-Luft- und eine Erdgas-Sauerstoff-Verbrennung. Für eine gegebene Nutzwärmeleistung in einem Feuerraum kann somit bei der Oxy-Fuel Verbrennung weniger Brennstoff eingesetzt werden als bei der Brennstoff-Luft-Verbrennung. Neben dem vermiedenen Stickstoff-Ballast im Abgas bei der Oxy-Fuel Feuerung verringert sich hierbei also die Abgasmenge noch weiter (Bild 3).
Bild 2: Feuerungstechnischer Wirkungsgrad bei Verbrennung von Erdgas mit Luft bzw. reinem Sauerstoff - Parameter: Lufttemperatur 20°C; Luftzahl=1,1; Brennstoff Erdgas L, Hu = 8,9 kWh/m3
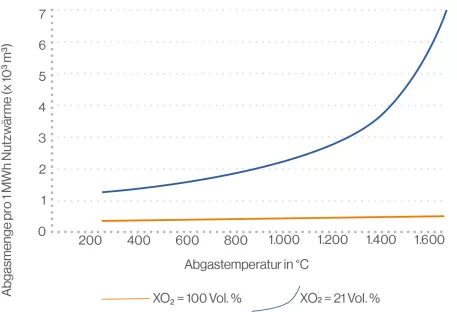
Bild 3: Abgasmenge einer Erdgas-Luft und einer Erdgas-Sauerstoff-Verbrennung, bezogen auf eine Nutzwärmeleistung von 1 MW - Parameter: Lufttemperatur 20°C; Luftzahl=1,1; Brennstoff Erdgas L, Hu = 8,9 kWh/m3
Detaillierte Informationen finden Sie in unserer Broschüre “Oxy-Fuel-Verbrennung - Grundlagen und Anwendungsbeispiele” (LINK Broschüre)
Wärmeübertragung auf das Wärmegut
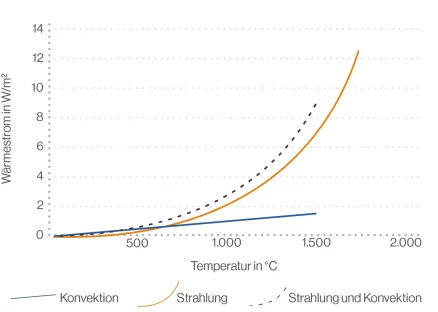
Im Temperaturbereich unter 800°C erfolgt die Wärmeübertragung von Flamme und Rauchgasen auf das Wärmegut hauptsächlich über Konvektion (Bild 4).
Da eine große Abgasmenge mit hoch turbulenten Strömungszustand günstig für einen hohen konvektiven Wärmeübergang ist, ist die hier Brennstoff-Luft-Verbrennung von Vorteil. Durch geeignete Maßnahmen wie der externen Rauchgas-Rezirkulation, bei der das durch den Ofenraum geschleuste Gasvolumen erheblich ansteigt, lässt sich der konvektive Wärmeübergang der Oxy-Fuel Verbrennung erheblich erhöhen.
Im Temperaturbereich oberhalb von 800°C dominiert die Wärmeübertragung durch Strahlung. Da das Rauchgas bei der Oxy-Fuel Verbrennung nahezu frei von Stickstoff ist und hauptsächlich aus CO₂ und H₂O besteht, ist der radiative Wärmeübertragungskoeffizient erheblich größer als bei der Brennstoff-Luft-Verbrennung (Stickstoff als symmetrisches Molekül nimmt nicht an der Wärmeübertragung durch Strahlung teil). Bei zusätzlicher Berücksichtigung der höheren Flammentemperatur bietet die Oxy-Fuel Verbrennung durch Strahlung also eine erheblich bessere Wärmeübertragung und ist der Brennstoff-Luft-Verbrennung in diesem Temperaturbereich klar überlegen. Diese Überlegenheit nimmt mit weiter steigenden Prozesstemperaturen weiter zu.
Bild 4: Wärmeübertragung durch Konvektion und Strahlung
NOx Bildung und NOx Emissionen
Die bei allen Verbrennungsvorgängen entstehenden Stickoxide (NOx Emissionen) schaden uns und unserer Umwelt (sie reizen die Atemwege und sind eine Ursache für sauren Regen). Die mit der Flamme entstehenden Stickoxide bilden sich auf drei unterschiedliche Arten:
1. NOx Bildung aus molekularem Stickstoff der Verbrennungsluft und eintretender Falschluft oder dem molekularen Stickstoffanteil des Brennstoffs (zum Beispiel Erdgas L). Stickoxide entstehen hierbei in den heißesten Zonen („thermisches NOx“).
2. NOx Bildung aus organisch gebundenen Stickstoffkomponenten des Brennstoffs (Fuel-NOx). Die Bildung von Stickoxid erfolgt über ein komplexes System zahlreicher chemischer Reaktionen. Brennstoffe mit organisch gebundenen Stickstoffkomponenten sind zum Beispiel schweres Heizöl und Kohle.
3. NOx Bildung aus molekularem Stickstoff über den Fuel-NOx-Mechanismus. Die auf diesem Weg gebildete Menge an NOx Emissionen ist klein und damit vernachlässigbar.
Die Bildung der Stickoxide erhöht sich mit steigender Temperatur erheblich. Modellrechnungen zeigen, dass eine nennenswerte NOx Bildung in realen Feuerungen ab etwa 1.300°C beginnt, da erst dann ausreichende Mengen an freien Sauerstoffradikalen vorliegen. Maßgeblich hierfür sind die maximal auftretende Flammentemperatur und die Temperaturspitzen.
Obwohl Oxy-Fuel Brenner als Oxidationsmedium nahezu stickstofffreien Sauerstoff nutzen, ist infolge der hohen Flammentemperaturen der Konversionsgrad zu NOx jedoch recht hoch. Das Abgas konventioneller Oxy-Fuel Brenner weist daher in der Regel höhere prozentuale NOx-Konzentrationen auf, jedoch ist aufgrund der geringen Abgasmenge die insgesamt emittierte Fracht an Stickoxid bei diesem Verfahren deutlich kleiner als bei Erdgas-Luft-Systemen.
NOx-arme Oxy-Fuel Brenner
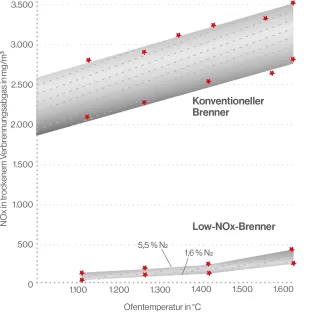
Air Liquide hat NOx-arme Brenner entwickelt, um die NOx-Emissionen von Oxy-Fuel Brennern zu verringern. Die wichtigste Maßnahme ist das Absenken der maximal auftretenden Flammentemperatur auf einen Wert möglichst nahe der Prozesstemperatur. Hierzu ist die interne und externe Abgas-Rezirkulation ein bewährtes Mittel.
In den Zonen mit hohen Temperaturen kann darüber hinaus der Sauerstoffpartialdruck und damit die NOx Bildung verringert werden. Der Vergleich eines NOx-armen Oxy-Fuel Brenners mit einem konventionellen zeigt bei einer Brennkammertemperatur von 1.400°C eine Reduktion der NOx-Werte um mehr als 90% (Bild 5).
Bild 5: NOx-Konzentration gerechnet als NO2 (trockenes Abgas, 3% O2) unter Einsatz von Erdgas
Die Vorteile der Oxy-Fuel Verbrennung auf einen Blick
- Besserer Wirkungsgrad (steigt weiter mit höherer Prozesstemperatur)
- Geringe Emissionen der Schadgase C02, CO, SOx, NOx
- Steigerung des Anteils von Ersatzbrennstoffen durch Sauerstoff unterstützte Verbrennung möglich
- Leistungssteigerung bei bestehenden Feuerungsanlagen
- Wesentlich verringerte Abgasmenge reduziert den Aufwand der Abgasreinigung erheblich
- Signifikant höhere radiative Wärmeübertragung
- Weiter sinkende NOx Emissionen durch den Einsatz NOx - armer Oxy-Fuel Brenner
- Geringerer Brennstoffverbrauch
Die Vorteile der Oxy-Fuel Verbrennung finden in vielen Industriezweigen wie der Metall-, Glas-, Keramik- und Zement-Industrie, aber auch in der Abfallverbrennung Anwendung.
Oxy-Fuel Brenner werden in unterschiedlichen Bauformen angeboten, zum Beispiel als metallische Brenner für Drehtrommelöfen und Lichtbogenöfen oder als keramischer Brenner für Glaswannen und Anwärmöfen. Zur Produktpalette gehören Oxy-Fuel Brenner für unterschiedliche flüssige und gasförmige Brennstoffe in einem breiten thermischen Leistungsbereich.
|
Aggregat |
Brenner-Bauform | Brennstoff | Leistungsbereich |
Metallindustrie |
Drehtrommelofen |
metallisch | flüssig / gasförmig | 0,5 - 6 MW |
Lichtbogenofen | gasförmig | 0,5 - 5 MW | ||
Konverter / Pfanne | flüssig / gasförmig | 0,5 - 4 MW | ||
Glasindustrie | Anwärmofen | keramisch | flüssig / gasförmig | 0,1 - 1MW |
Glaswanne | flüssig / gasförmig | 0,2 - 4 MW | ||
Keramikindustrie | Drehtrommelofen | metallisch | flüssig / gasförmig | 0,5 - 5 MW |
Herdofen | keramisch | gasförmig | 0,5 - 5 MW | |
Zementindustrie | Drehrohrofen | metallisch | flüssig / gasförmig Ersatzbrennstoffe |
2 - 5 MW |
Kalzinierer | flüssig / gasförmig | 2 - 5 MW | ||
Thermische |
Klärschlamm Wirbelschichtofen |
metallisch | gasförmig | 0,5 - 6 MW |
Sonderabfall Drehrohrofen Nachbrennkammer |
flüssig | 0,5 - 6 MW |