Versteckte Kosten beim Schutzgasschweißen: Optimierungspotentiale durch reproduzierbare Versuche
Die Prozesskosten beim Schutzgasschweißen werden im Wesentlichen durch:
- die Wahl des Verfahrens
- die Anlagenkosten (Schweißgerät)
- den Werkstoff
- die Materialstärke
- die Güteanforderungen
- die Produktivität in der Ausführung
- Nahtfehler
- und Nacharbeit verursacht
Die Produktivität hängt wesentlich von der Abschmelzleistung des gewählten Verfahrens bzw. von der Einschaltdauer beim konkreten Einsatz ab und wird zumeist in m/min oder kg/h gemessen. Zusätzlichen Einfluss haben die Schweißnahtvorbereitung und der Aufwand durch Nacharbeiten.
Einflussfaktoren auf die Abschmelzleistung sind:
- Die Stromquelle und deren eingestellte Parameter
- Die Schweißposition bzw. Art und Zugänglichkeit der Schweißnaht und
- die nötigen Hilfsstoffe (z.B. Schutzgase)
Abgestimmt auf die vorab definierten Ziele und unter Berücksichtigung etwaiger Restriktionen wird im Versuchsablauf der Einfluss einzelner Parametervariationen auf:
- Lichtbogenform
- Tropfenbildung
- Werkstoffübergang
- Schmelzdynamik
- Benetzung
- Erstarrung
- die Bildung von Spritzern, Rauch, Schmauch und Partikeln
usw. analysiert.
Häufig sind wesentliche Parameter vorgegeben (Werkstoff, Schweißzusatz, etc.), sodass sich über die Anpassung des Schutzgases ein zusätzlicher und wesentlicher Freiheitsgrad zur Optimierung bestehender Prozesse ergibt.
Wussten Sie, dass die Kosten für Hilfsstoffe wie das Schutzgas typischerweise weniger als 5% der gesamten Prozesskosten beträgt?
Gleichzeitig kann die Wahl des optimalen Schutzgases die Produktivität erheblich steigern und die Nacharbeit verringern – und das ohne zusätzliche Investition.
Schweißfehler: Ursachen erkennen und vermeiden
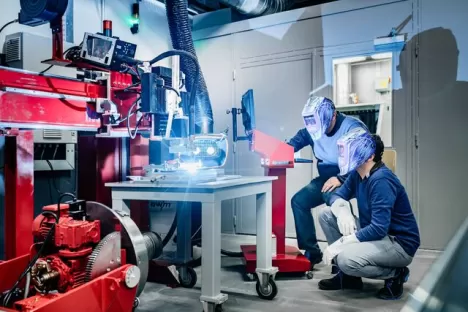
Der Einfluss der handwerklichen Fertigkeit des ausführenden Schweißers wird durch automatisiertes Schweißen vermieden. Die automatische Prozessdatenerfassung mit synchronen High Speed Aufnahmen einer Spezialkamera ermöglichen einen Einblick in den Lichtbogen und damit in den Moment der Entstehung des Schweißnahtaufbaus.
Der Versuchsablauf und die Ergebnisse sind transparent und reproduzierbar.
Zerstörungsfreie Untersuchung: Sichtprüfung Schweißnaht
Hier beginnt der Bereich der “Wahrheit”, denn die Veränderung eines Schweißprozesses hat immer einen Einfluss auf die Nahtqualität, den Nahtaufbau und die Metallurgie des Werkstoffs im Bereich der Schweißnaht. Dabei ist aus werkstoff technischer Sicht das Ziel maßgeblich, so weit wie möglich die Eigenschaften des Ausgangswerkstoffs (Grundwerkstoff) bzw. Aufbauwerkstoffes (Cladding/Auftragswerkstoff) zu erreichen oder gezielt neue Eigenschaften aufzubauen.
Die Wirkungen sind mit reiner äußerlicher Betrachtung ohne Hilfsmittel in der Regel nicht festzustellen.
Deshalb werden die Schweißnähte und Bauteile umfassend untersucht. Bei der zerstörungsfreien Untersuchung arbeiten wir zunächst mit
- Sichtprüfungen,
- Farbeindringprüfung,
- Röntgen/Durchstrahlung
- und zusätzlicher Lichtmikroskopie.
Die bis zu 1000-fache Vergrößerung von Strukturen erlaubt es, Details sichtbar zu machen, die ohne Hilfsmittel für das menschliche Auge verborgen bleiben.
Optisch erkennbare Einflüsse wie zum Beispiel Risse, Poren oder Oberflächenfehler (Einbrandkerben, Benetzungsfehler) können so präzise beurteilt werden.
Zur Bestimmung der Schweißnahtzusammensetzung und des Werkstoffaufbaus werden an der Oberfläche Ferritbestimmungen und Werkstoffanalysen durchgeführt.
Je nach Anforderung kann eine Durchstrahlungsprüfung mittels Röntgenstrahlung als weitere zerstörungsfreie Werkstoffprüfung genutzt werden, um typische Schweißfehler wie Bindefehler, Risse, Porosität, Lunker, Einschlüsse oder unzureichende Durchschweißungen sichtbar zu machen.
Hierfür steht ein eigener Röntgenraum zur Verfügung.
Zerstörende Schweißnahtprüfung
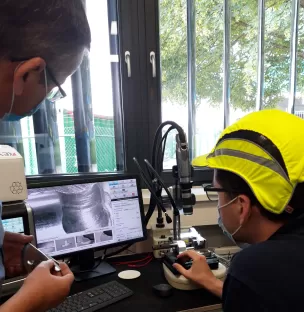
Die zerstörende Prüfung ist der Blick ins Innere der Schweißnaht.
Dabei erfolgt zunächst die Probenaufbereitung in dieser Reihenfolge:
- Trennen
- Einbetten
- Schleifen & Polieren
- Ätzen
Trennen
Beschreibt das mechanische Heraustrennen von interessanten Bauteilbereichen für weitere Präparationsschritte und Analysen.
Einbetten
Durch das Einbetten der Proben wird in erster Linie eine bessere Handhabung für die anschließende Präparation und Auswertung erreicht.
Schleifen & Polieren
Das Schleifen erfolgt, um die Bearbeitungsschicht, die bei der Probeentnahme entstanden ist, zu entfernen und um die Probe für die weitere Präparation vorzubereiten. Der Schleifvorgang wird in mehreren Schritten ausgeführt und erfordert Geschick und Erfahrung. Es kommen Schleifpapiere grober bis sehr feiner Körnung zum Einsatz.
Um höchste Oberflächengüten zu erreichen, können die Proben nach dem Schleifen noch zusätzlich poliert werden.
Ätzen
In der Regel ist eine Kontrastierung des Gefüges durch Ätzen notwendig, um die verschiedenen Gefügebestandteile sichtbar zu machen. Dabei wird die Tatsache genutzt, dass der chemische Angriff bei den Gefügebestandteilen von deren Orientierung und deren chemischer Zusammensetzung abhängt.
Beurteilung der Schweißnahtgüte anhand der Werkstoffeigenschaften
Im ersten Schritt erfolgt wieder eine lichtmikroskopische Untersuchung des Schliffbilds. Im Gegensatz zur zerstörungsfreien Untersuchung lassen sich jetzt Effekte im Inneren der Schweißnaht wie Rissbildung, Poren und der Verlauf der Wärmeeinflusszone gut erkennen.
Markante Bereiche können markiert, vermessen und zur besseren Erkennbarkeit kontrastiert und digital abgespeichert werden. Hierzu wird ein Lichtmikroskop mit Digital Imaging (Vergrößerung bis ca. 200x) eingesetzt.
Die Beurteilung geätzter Schliffbilder erlaubt Aussagen, über die beim Schweißprozess gebildeten Gefügebestandteile. Die Auswertung der Korngröße gibt eine indirekte Möglichkeit, die lokalen Temperaturen, die beim Schweißen geherrscht haben, abzuschätzen.
Da die Qualität einer Schweißverbindung entscheidend von der Phasenzusammensetzung des Werkstoffs bestimmt wird, steht hierfür ein Feritscope zur Verfügung, das nach dem magnetinduktiven Messprinzip den prozentualen Anteil ferromagnetischer Bestandteile ermittelt.
Ein Mangel an Ferrit im Schweißnahtbereich führt zu einer Verringerung der Festigkeit; demgegenüber führt ein zu hoher Ferritgehalt zur Reduzierung der Zähigkeit. Festigkeit und Zähigkeit bestimmen wesentlich die mechanischen Eigenschaften und damit die Werkstoffgüte.
Außerdem können mit diesem Messgerät Schweißnähte in polierten Oberflächen ausfindig gemacht werden.
Bei den meisten technisch relevanten Metallen handelt es sich um Legierungen, also Stoffgemische aus mehreren chemischen Elementen. Da die Werkstoffeigenschaften essentiell von der chemischen Zusammensetzung bestimmt werden, ist die Analyse der genauen Werkstoffzusammensetzung ein wesentlicher Schritt der Materialuntersuchung.
Das Funkenspektrometer bietet die Möglichkeit, die genaue chemische Zusammensetzung aller metallischen Werkstoffe zu bestimmen.
Die Härte, die als Widerstand gegen das Eindringen eines Fremdkörpers definiert ist, ist eine der wichtigsten Werkstoffeigenschaften. Darüber hinaus verhält sich die Härte eines Metalls in vielen Fällen proportional zur Festigkeit und Verschleißbeständigkeit und antiproportional zur Verformbarkeit.
Durch das Vermessen von Härteverläufen in Schweißnähten können vielfältige Aussagen über die Qualität der Fügeverbindung gemacht werden. Harte und somit spröde Bereiche sowie Wärmeeinflusszonen – die in den meisten Fällen eine geringe Härte aufweisen – können mit der Härteprüfung detektiert werden.